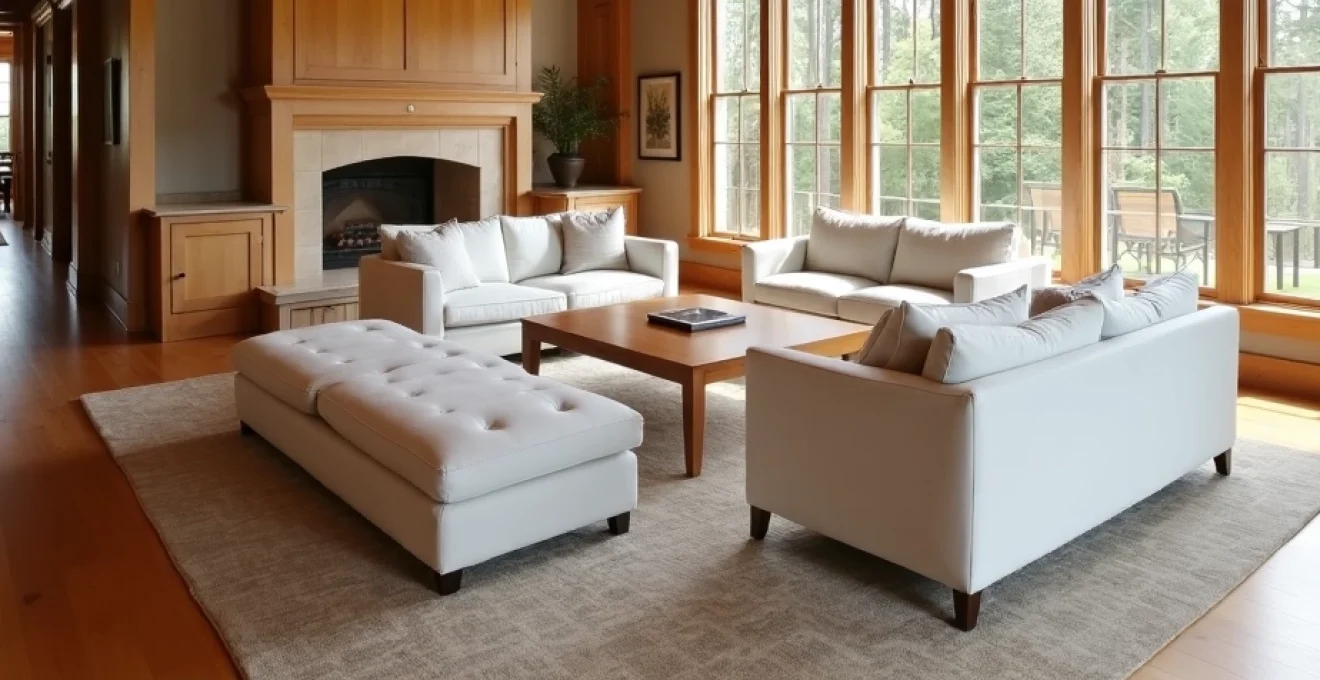
Custom carpentry and joinery have long been revered as the pinnacle of craftsmanship in interior design. These specialized skills transform raw materials into bespoke elements that elevate spaces from ordinary to extraordinary. By combining traditional techniques with modern innovations, skilled artisans can create unique, functional, and aesthetically pleasing interiors that reflect the personality and needs of their occupants.
The art of custom woodworking goes beyond mere furniture making; it encompasses the creation of architectural features, built-in elements, and intricate details that define the character of a space. From hand-carved moldings to precisely fitted cabinetry, the possibilities are limitless when it comes to crafting interiors that stand out for their elegance and individuality.
Fundamentals of custom carpentry and joinery techniques
At the heart of custom carpentry and joinery lies a deep understanding of wood properties, precision cutting, and assembly techniques. These fundamental skills form the foundation upon which master craftsmen build their expertise. The ability to select the right wood, prepare it properly, and join pieces seamlessly is crucial for creating durable and beautiful custom elements.
One of the most critical aspects of carpentry is the ability to create strong, stable joints that can withstand the test of time. Traditional joinery methods, such as mortise and tenon, dovetail, and finger joints, are still widely used today for their strength and aesthetic appeal. These techniques allow for the creation of furniture and built-ins that are not only sturdy but also showcase the skill of the craftsman.
Modern technology has also found its place in custom carpentry, with computer-aided design (CAD) and computer numerical control (CNC) machines enabling greater precision and efficiency in certain aspects of the work. However, the human touch remains irreplaceable, especially when it comes to the final fitting and finishing of custom pieces.
Wood selection and preparation for bespoke interior elements
The selection of wood is a critical first step in any custom carpentry project. Different species of wood offer varying characteristics in terms of grain pattern, color, hardness, and workability. Understanding these properties allows craftsmen to choose the best material for each specific application, ensuring both functionality and aesthetic appeal.
Hardwoods vs. softwoods: optimal choices for different applications
Hardwoods, derived from deciduous trees, are generally denser and more durable than softwoods, which come from coniferous trees. Oak, maple, walnut, and cherry are popular hardwoods prized for their strength and beautiful grain patterns, making them ideal for furniture and high-wear surfaces. Softwoods like pine and cedar are lighter, more affordable, and easier to work with, often used for structural elements and in rustic or casual designs.
The choice between hardwoods and softwoods depends on various factors, including the intended use, budget, and desired aesthetic. For example, a custom dining table might benefit from the durability and rich appearance of walnut, while a set of built-in bookshelves could be crafted from pine and painted to match the room's decor.
Quarter-sawn and rift-sawn lumber for stability and aesthetics
The way lumber is cut from a log can significantly impact its stability and appearance. Quarter-sawn and rift-sawn boards are prized for their dimensional stability and unique grain patterns. These cutting methods minimize wood movement due to changes in humidity, making them ideal for applications where warping or twisting could be problematic, such as cabinet doors or table tops.
Quarter-sawn lumber exhibits a straight grain pattern with distinctive ray flecks, particularly visible in species like oak. This not only adds visual interest but also increases the wood's resistance to cupping and twisting. Rift-sawn wood offers a similar stability with a more uniform, linear grain pattern, perfect for contemporary designs that prioritize clean lines.
Acclimatization and moisture content management in woodworking
Wood is a hygroscopic material, meaning it absorbs and releases moisture in response to its environment. Proper acclimatization of wood before and during the construction process is crucial to prevent warping, splitting, or joint failure in the finished piece. Craftsmen must allow wood to reach equilibrium moisture content with its intended environment before beginning work.
Moisture meters are essential tools in a woodworker's arsenal, allowing for precise monitoring of wood moisture content. Ideally, interior wood should have a moisture content between 6% and 8% for optimal stability. Controlling the workshop environment through humidity regulation and proper storage practices helps maintain consistent moisture levels throughout the project.
Sustainable timber sources: FSC-certified and reclaimed wood options
As environmental consciousness grows, many clients and craftsmen are turning to sustainable wood sources for their projects. Forest Stewardship Council (FSC) certification ensures that wood products come from responsibly managed forests that provide environmental, social, and economic benefits. Using FSC-certified wood allows for the creation of beautiful, custom pieces with a clear conscience.
Reclaimed wood has also gained popularity in custom carpentry and joinery. This material, salvaged from old buildings, barns, or industrial structures, brings a unique character and history to new projects. Working with reclaimed wood requires additional skill to address potential issues like embedded nails or varying moisture content, but the results can be stunning, offering a blend of sustainability and vintage charm.
Advanced joinery methods for furniture and built-ins
The art of joinery is what sets apart fine woodworking from basic carpentry. Advanced joinery methods not only provide structural integrity but also contribute to the overall aesthetic of the piece. Mastering these techniques allows craftsmen to create furniture and built-ins that are both beautiful and enduring.
Dovetail variations: through, half-blind and secret mitered dovetails
Dovetail joints are renowned for their strength and decorative quality. The interlocking "tails" and "pins" create a joint that resists pulling apart, making it ideal for drawers and box construction. Through dovetails, where both elements are visible on the sides of the joint, showcase the craftsman's skill and are often featured in high-end furniture.
Half-blind dovetails conceal one side of the joint, commonly used where the side of a drawer meets the front. This technique combines strength with a cleaner appearance from the front view. For the ultimate in subtlety, secret mitered dovetails hide the joint entirely, presenting a seamless mitered corner while maintaining the strength of a dovetail internally.
Mortise and tenon joints: floating, wedged and tusk tenon applications
The mortise and tenon joint is a fundamental technique in woodworking, used for centuries to join pieces at right angles. This strong joint is commonly found in frame construction, such as in doors, windows, and furniture legs. Variations like the floating tenon allow for easier assembly and greater flexibility in design.
Wedged tenons add both strength and visual interest to a joint. By cutting a slot in the end of the tenon and inserting a wedge, the joint is locked in place and resistant to pulling apart. Tusk tenons, often seen in trestle table designs, use a removable wedge to allow for easy disassembly, combining practicality with traditional aesthetics.
Splined miter joints for decorative and structural integrity
Miter joints, where two pieces meet at an angle (typically 45 degrees), can be strengthened and beautified with the addition of splines. These thin strips of wood, inserted across the joint, not only reinforce the connection but also add a decorative element. Contrasting wood species for splines can create striking visual effects, particularly in picture frames or box corners.
The use of splined miter joints demonstrates a high level of craftsmanship and attention to detail. This technique is particularly valuable in applications where the joint may be subject to stress or where a clean, seamless appearance is desired with added structural integrity.
Japanese-inspired joinery: Kumiko and Shoji screen techniques
Japanese woodworking traditions have long been admired for their precision and beauty. Kumiko, a technique involving the assembly of small wooden pieces into intricate patterns without the use of nails or glue, has gained popularity in contemporary custom woodworking. These delicate lattice designs can be incorporated into cabinet doors, room dividers, or decorative panels, adding a touch of elegance and craftsmanship to any interior.
Shoji screens, traditionally used in Japanese architecture as room dividers or windows, employ a frame and panel construction that can be adapted for various custom carpentry applications. The principles behind shoji construction, emphasizing lightness and modularity, can inspire innovative solutions for modern interiors, such as sliding doors or decorative wall panels.
Custom cabinetry design and construction
Custom cabinetry is often the centerpiece of interior woodworking projects, offering both functionality and aesthetic appeal. The design and construction of bespoke cabinets require a deep understanding of space utilization, ergonomics, and material properties to create storage solutions that are both beautiful and practical.
Face-frame vs. frameless cabinet construction methods
Two primary methods dominate cabinet construction: face-frame and frameless (also known as European-style). Face-frame cabinets feature a frame attached to the front of the cabinet box, providing structure and a mounting point for doors and drawers. This traditional method offers a classic look and allows for easy adjustment of door alignment.
Frameless cabinets, on the other hand, rely on a thicker box construction without a face frame. This style provides a sleek, modern appearance and maximizes interior space. The choice between these methods often depends on the desired aesthetic and functional requirements of the project. Some designers even combine elements of both styles to create unique, hybrid solutions tailored to specific needs.
Drawer box fabrication: dovetailed vs. lock-joint assemblies
The construction of drawer boxes is a crucial aspect of cabinetry that impacts both durability and aesthetics. Dovetail joints, with their interlocking pins and tails, are widely regarded as the premium choice for drawer construction. These joints offer superior strength and a distinctive appearance that signifies quality craftsmanship.
Lock-joint assemblies, also known as finger joints, provide a strong alternative to dovetails. While perhaps not as visually striking, lock joints offer excellent durability and can be more cost-effective to produce. For painted drawers or in less visible areas, lock joints can be an efficient choice without compromising on quality.
Hardware integration: concealed hinges and soft-close mechanisms
The integration of modern hardware can significantly enhance the functionality and user experience of custom cabinetry. Concealed hinges, which are hidden from view when the cabinet is closed, offer clean lines and a sleek appearance. These hinges often provide adjustability in three dimensions, allowing for precise alignment of doors.
Soft-close mechanisms have become increasingly popular in high-end cabinetry. These devices ensure that doors and drawers close gently and quietly, preventing slamming and reducing wear and tear. The incorporation of such hardware demonstrates attention to detail and a commitment to both form and function in custom carpentry work.
Veneering techniques for high-end cabinet surfaces
Veneering is a technique that allows craftsmen to create stunning cabinet surfaces using thin slices of premium wood. This method not only conserves valuable hardwoods but also enables the creation of intricate patterns and book-matched panels that would be impossible or prohibitively expensive with solid wood.
Advanced veneering techniques, such as marquetry and parquetry, involve creating decorative patterns or pictures using different wood species or cuts. These highly skilled processes can transform cabinet doors or drawer fronts into works of art, adding a luxurious touch to custom cabinetry.
Architectural woodworking for elegant interiors
Architectural woodworking plays a crucial role in defining the character and style of interior spaces. From decorative wall treatments to functional built-ins, these elements contribute significantly to the overall atmosphere and functionality of a room. Custom architectural woodwork allows for the creation of unique features that perfectly complement the architecture and design vision of a space.
Wainscoting styles: raised panel, flat panel and beadboard designs
Wainscoting is a classic wall treatment that adds depth, texture, and elegance to interior spaces. Raised panel wainscoting, characterized by its three-dimensional panels framed by stiles and rails, offers a traditional, formal appearance often seen in dining rooms and studies. This style requires precise cutting and assembly to ensure that panels fit snugly within their frames.
Flat panel wainscoting provides a more contemporary look while still offering the decorative benefits of wall paneling. This style is versatile and can be adapted to various interior design themes. Beadboard, with its distinctive vertical grooves, brings a casual, cottage-like charm to spaces and is particularly popular in kitchens and bathrooms.
Crown molding profiles and installation techniques
Crown molding serves as the finishing touch in many interiors, bridging the gap between walls and ceilings with decorative profiles. The selection of the appropriate crown molding profile depends on factors such as ceiling height, room proportions, and overall design style. Custom carpentry allows for the creation of unique molding profiles that perfectly complement the architecture of a space.
Installation of crown molding requires skill and precision, particularly when dealing with corners and transitions. Techniques such as coping, which involves cutting one piece to fit the profile of another, ensure tight, seamless joints. In rooms with complex geometry or historical features, custom fabrication of molding sections may be necessary to achieve a cohesive look.
Custom wooden staircases: balustrades and newel post fabrication
Staircases often serve as focal points in homes and can be transformed into stunning architectural features through custom carpentry. The design and fabrication of balustrades (the system of railings and balusters) and newel posts (the larger supporting posts) offer opportunities for creative expression and craftsmanship.
Turned balusters, carved newel posts, and intricately designed handrails can elevate a staircase from a functional element to a work of art. The integration of different wood species, metalwork, or glass can create unique, contemporary designs that serve as striking visual elements within the home.
Built-in bookcases and window seats with integrated storage
Built-in elements like bookcases and window seats not only provide functional storage but also contribute to the architectural character of a space. Custom bookcases can be designed to fit perfectly within alcoves or along walls, maximizing storage capacity while complementing the room's proportions and style.
Window seats with integrated storage offer a charming addition to bedrooms, living rooms, or kitchens. These built-ins take advantage of often underutilized space beneath windows, creating cozy nooks for reading or relaxation while providing hidden storage for books, blankets, or other items. The ability to customize these elements ensures that they meet both the functional needs and aesthetic preferences of the homeowner.
Finishing techniques for custom woodwork
The finishing process is the final, crucial step in custom woodworking that can dramatically enhance the beauty of the wood and protect it for years to come. Different finishing techniques can highlight the natural grain, add color, or create specific textures and effects that complement the overall design of the piece and the space it inhabits.
French polishing for high-gloss, mirror-like finishes
French polishing is a traditional finishing technique that produces a high-gloss, luxurious surface particularly suited to fine furniture and decorative woodwork. This labor-intensive process involves applying many thin layers of shellac using a special rubbing pad, building up a deep, lustrous finish that enhances the wood's natural beauty.
The French polish technique requires significant skill and patience, as each layer must be carefully applied and allowed to dry before the next is added. The result is a finish with unparalleled depth and clarity, often described as having a "piano finish" due to its association with high-end musical instruments.
Cerused oak and wire-brushed textures for rustic elegance
Cerused oak, also known as limed oak, is a finishing technique that involves applying a light-colored pigment to oak wood, emphasizing the grain pattern. This creates a striking contrast between the light pigment in the pores and the darker wood surface. The effect adds depth
and texture to woodwork, creating a rustic yet sophisticated appearance that's particularly popular in contemporary and transitional interior designs.Wire-brushing is another technique that enhances the natural texture of wood. This process involves using a wire brush to remove the softer wood between the grain, creating a tactile surface that highlights the wood's natural pattern. When combined with staining or cerusing, wire-brushed textures can produce stunning finishes that are both visually and tactilely appealing.
Milk paint and chalk paint applications for antique effects
Milk paint and chalk paint have gained popularity for their ability to create an authentic aged or antique appearance on woodwork. Milk paint, made from milk protein, lime, and pigments, has been used for centuries and is known for its matte, slightly textured finish. When applied to raw wood, it can penetrate the surface, creating a durable finish that mimics the look of well-worn antique furniture.
Chalk paint, a more modern invention, offers similar aesthetic qualities to milk paint but with easier application and versatility. It adheres well to most surfaces without priming and can be distressed easily to create a vintage look. Both milk and chalk paints can be sealed with wax or other finishes to enhance durability while maintaining their characteristic matte appearance.
Spray finishing with conversion varnishes and catalyzed lacquers
For projects requiring a highly durable, smooth finish, spray application of conversion varnishes or catalyzed lacquers is often the preferred method. These finishes offer superior resistance to scratches, chemicals, and moisture, making them ideal for high-use surfaces like kitchen cabinets and table tops.
Conversion varnishes undergo a chemical reaction when applied, resulting in a hard, durable finish. Catalyzed lacquers, which come in pre-catalyzed and post-catalyzed varieties, offer similar durability with faster drying times. The spray application of these finishes requires skill and proper equipment but results in a flawless, professional-grade finish that enhances the beauty of the woodwork while providing long-lasting protection.