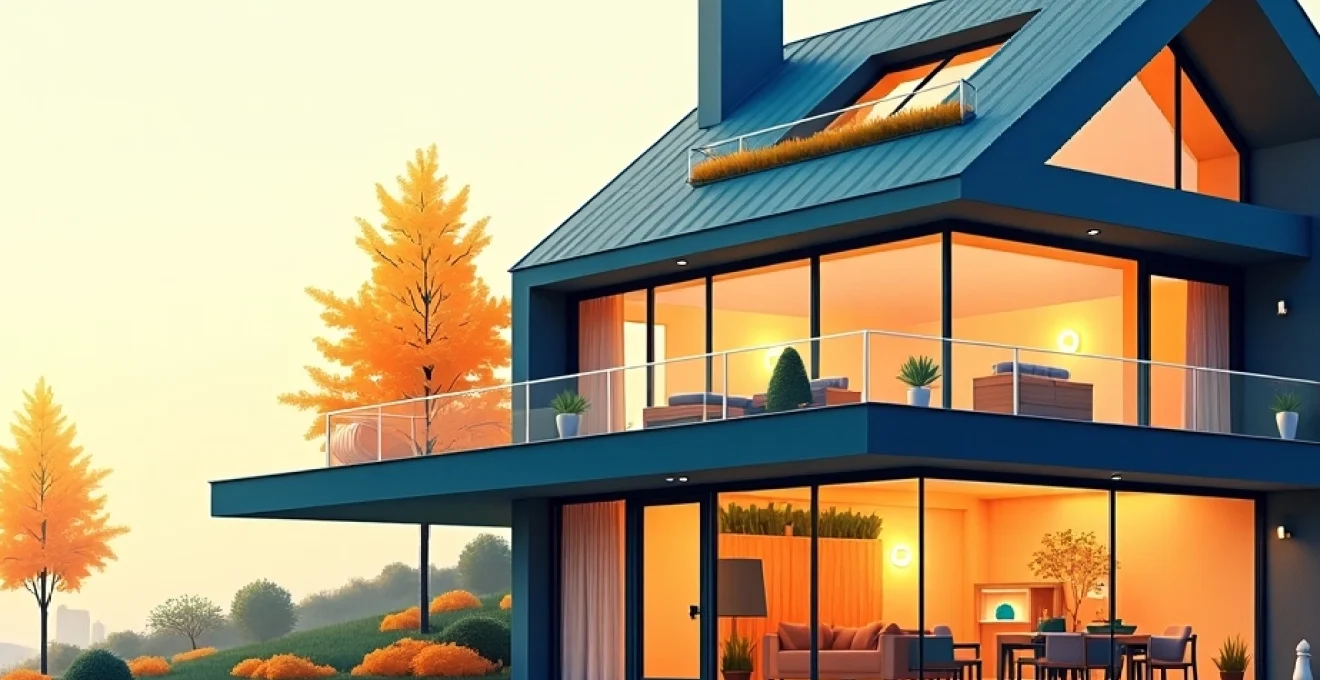
In the quest for sustainable and energy-efficient living, passive houses have emerged as a groundbreaking solution. These cutting-edge buildings represent the pinnacle of architectural design and engineering, offering unparalleled insulation and energy performance. By leveraging advanced construction techniques and innovative materials, passive houses create comfortable living spaces while dramatically reducing energy consumption. As global awareness of climate change grows and energy costs continue to rise, the principles behind passive house design are gaining traction worldwide, reshaping the future of residential and commercial construction.
Fundamental principles of passive house design
Passive house design is built upon a set of core principles that work in harmony to create highly efficient, comfortable, and sustainable buildings. These principles focus on maximizing energy conservation and minimizing heat loss, resulting in structures that require minimal heating and cooling. The foundation of passive house design lies in creating an airtight, well-insulated envelope that maintains a consistent indoor temperature regardless of external conditions.
One of the key aspects of passive house design is the emphasis on passive heating and cooling strategies. This means utilizing natural sources of heat, such as sunlight and internal heat gains from occupants and appliances, while minimizing heat loss through the building envelope. By carefully orienting the building and strategically placing windows, passive houses can take full advantage of solar heat gain during colder months while minimizing unwanted heat during warmer periods.
Another crucial element is the use of high-performance insulation throughout the building envelope. This includes walls, roofs, and foundations, creating a continuous thermal barrier that significantly reduces heat transfer between the interior and exterior. The goal is to achieve a level of insulation that far exceeds traditional building standards, often resulting in walls that are several times thicker than those found in conventional construction.
Advanced insulation techniques in passive houses
Passive houses employ a range of advanced insulation techniques to achieve their exceptional energy performance. These methods go beyond simply adding more insulation material and instead focus on creating a comprehensive system that eliminates thermal bridges and maximizes the effectiveness of the insulation layer.
Superinsulation and thermal bridge-free construction
Superinsulation is a cornerstone of passive house design, involving the use of high-performance insulation materials and techniques to create an extremely efficient thermal envelope. This approach typically results in insulation levels that are 2-3 times higher than those required by standard building codes. The goal is to achieve R-values (a measure of thermal resistance) that can exceed R-40 for walls and R-60 for roofs in colder climates.
Equally important is the concept of thermal bridge-free construction. Thermal bridges are areas in the building envelope where heat can easily transfer between the interior and exterior, bypassing the insulation layer. Common thermal bridges include wall studs, window frames, and balcony connections. Passive house design aims to eliminate or minimize these thermal bridges through careful detailing and the use of specialized components.
High-performance windows and glazing systems
Windows are often the weakest link in a building's thermal envelope, but in passive houses, they become a powerful tool for energy efficiency. Passive house windows typically feature triple-pane glazing with low-emissivity coatings and inert gas fills between the panes. These high-performance windows can achieve U-values (a measure of heat transfer) as low as 0.15 W/(m²K), significantly outperforming standard double-pane windows.
The frames of passive house windows are also carefully designed to minimize thermal bridging. Many use composite materials or incorporate thermal breaks to reduce heat transfer through the frame itself. The installation of these windows is equally critical, with careful attention paid to sealing and insulating around the window openings to maintain the integrity of the building envelope.
Airtight building envelope strategies
Achieving an airtight building envelope is crucial for passive house performance. Air leakage can account for a significant portion of heat loss in traditional buildings, but passive houses aim to reduce this to near zero. The target air change rate for a passive house is typically no more than 0.6 air changes per hour at 50 Pascals of pressure, as measured by a blower door test.
To achieve this level of airtightness, passive houses employ a continuous air barrier throughout the entire building envelope. This barrier is carefully detailed at all joints, penetrations, and transitions to ensure there are no gaps or leaks. Common materials used for the air barrier include specialized membranes, tapes, and sealants designed for long-term durability and performance.
Insulated concrete forms (ICF) and structural insulated panels (SIP)
Innovative construction systems like insulated concrete forms (ICF) and structural insulated panels (SIP) are often employed in passive house construction due to their superior insulation properties and ability to create a continuous thermal envelope. ICFs consist of hollow foam blocks that are stacked and filled with concrete, creating a wall system with excellent insulation and thermal mass properties. SIPs, on the other hand, are prefabricated panels consisting of an insulating foam core sandwiched between two structural boards, offering high insulation values and rapid assembly on-site.
These systems not only provide excellent thermal performance but also contribute to the overall airtightness of the building envelope. By reducing the number of joints and connections in the structure, ICFs and SIPs help minimize potential air leakage paths and simplify the creation of a continuous air barrier.
Mechanical ventilation with heat recovery (MVHR) systems
Given the airtight nature of passive houses, proper ventilation becomes critically important to maintain indoor air quality and comfort. This is where mechanical ventilation with heat recovery (MVHR) systems play a vital role. MVHR systems provide a constant supply of fresh air while recovering heat from the exhaust air, ensuring energy efficiency and optimal indoor air quality.
Core components of MVHR units
An MVHR system consists of several key components working together to provide efficient ventilation. The heart of the system is the heat exchanger, which transfers heat from the outgoing stale air to the incoming fresh air. This process can recover up to 90% of the heat that would otherwise be lost through ventilation.
Other essential components include:
- Fans for air circulation
- Filters to remove particulates and pollutants
- Ducting for air distribution
- Control systems for managing airflow and operation
These components work in concert to ensure a constant supply of fresh, filtered air throughout the building while maintaining energy efficiency.
Efficiency ratings and heat recovery effectiveness
The efficiency of MVHR systems is typically measured by their heat recovery efficiency and their specific fan power (SFP). Heat recovery efficiency indicates the percentage of heat that is recovered from the exhaust air and transferred to the incoming fresh air. High-quality MVHR units can achieve heat recovery efficiencies of 85-95%.
Specific fan power is a measure of the electrical energy required to move a given volume of air. Lower SFP values indicate more efficient operation. Passive house standards typically require MVHR systems to have an SFP of less than 0.45 W/(m³/h) to ensure energy-efficient operation.
Integration with passive solar design
MVHR systems in passive houses are often integrated with passive solar design principles to maximize overall energy efficiency. For example, the system can be programmed to take advantage of solar heat gains during winter months by reducing the ventilation rate when the sun is warming the interior spaces. Conversely, during summer nights, the system can increase ventilation to flush out warm air and cool the building using cooler nighttime temperatures.
This integration of active and passive systems allows for optimal energy performance and comfort control throughout the year, adapting to changing environmental conditions and occupant needs.
Energy performance metrics and certification standards
The performance of passive houses is rigorously evaluated using specific metrics and certification standards. These criteria ensure that buildings marketed as passive houses truly deliver on their promises of exceptional energy efficiency and comfort.
Passive house institute (PHI) criteria and certification process
The Passive House Institute (PHI) has established a set of stringent criteria that buildings must meet to achieve Passive House certification. These criteria include:
- Space Heating Energy Demand: ≤ 15 kWh/(m²a) or 10 W/m² peak demand
- Space Cooling Energy Demand: Roughly matches the heating demand with an additional allowance for dehumidification
- Primary Energy Renewable (PER) Demand: ≤ 60 kWh/(m²a)
- Airtightness: ≤ 0.6 air changes per hour at 50 Pascals pressure
- Thermal Comfort: Not more than 10% of hours in a year > 25°C
The certification process involves detailed documentation of the building design, energy modeling, and on-site testing to verify compliance with these criteria. This rigorous process ensures that certified Passive Houses deliver consistent, high-level performance.
PHPP (passive house planning package) software modeling
The Passive House Planning Package (PHPP) is a sophisticated energy modeling tool developed by the Passive House Institute. This software is used to simulate the energy performance of a building design and verify compliance with Passive House standards. PHPP takes into account a wide range of factors, including climate data, building geometry, insulation levels, window specifications, and mechanical systems.
Using PHPP, designers can optimize their building designs to achieve Passive House performance levels. The software provides detailed insights into energy flows within the building, allowing for fine-tuning of various design elements to maximize efficiency. PHPP modeling is a required step in the Passive House certification process and serves as a valuable tool for predicting and optimizing building performance.
Primary energy renewable (PER) factor assessment
The Primary Energy Renewable (PER) factor is a metric used in Passive House certification to assess the overall energy efficiency of a building, taking into account the source of the energy used. This approach considers not just the energy consumed on-site, but also the energy required to produce and deliver that energy to the building.
The PER factor takes into account the efficiency of different energy sources and the potential for renewable energy integration. By using this metric, Passive House certification encourages the use of efficient, renewable energy sources and promotes a holistic approach to energy consumption in buildings.
Cost-benefit analysis of passive house construction
While the initial cost of constructing a passive house can be higher than that of a conventional building, the long-term benefits often outweigh this initial investment. The cost premium for passive house construction typically ranges from 5-10% above standard construction costs, depending on the specific design and local market conditions.
However, the energy savings achieved by passive houses can be substantial. Many passive houses report energy consumption reductions of 80-90% compared to conventional buildings. Over the lifecycle of the building, these energy savings can more than offset the initial cost premium.
Additionally, passive houses offer several other benefits that contribute to their overall value:
- Improved indoor air quality and comfort
- Reduced maintenance costs due to high-quality components
- Increased property value and marketability
- Enhanced resilience to power outages and extreme weather events
- Lower carbon footprint and environmental impact
When considering these factors, passive house construction often represents a sound financial investment, particularly for those with a long-term perspective on building ownership and operation.
Case studies: exemplary passive house projects worldwide
Passive house principles have been successfully applied in a wide range of projects around the world, demonstrating their versatility and effectiveness in various climates and building types.
Bedzed eco-village in London, UK
The Beddington Zero Energy Development (BedZED) in London is a pioneering eco-village that incorporates many passive house principles. Completed in 2002, BedZED features 100 homes, office spaces, and community facilities designed to achieve zero carbon emissions. The project uses super-insulation, triple-glazed windows, and passive solar design to minimize energy demand. While not officially certified as a Passive House, BedZED has achieved significant energy reductions and serves as an early example of large-scale sustainable community design.
Smith House in Urbana, Illinois, USA
The Smith House, completed in 2012, is one of the first certified Passive Houses in Illinois. This single-family home demonstrates that passive house principles can be successfully applied in the challenging climate of the American Midwest, with its hot summers and cold winters. The house features 14-inch thick walls filled with cellulose insulation, triple-pane windows, and a highly efficient MVHR system. Despite its extreme climate, the Smith House maintains comfortable indoor temperatures year-round with minimal energy input.
Bruck passive house apartment complex in China
The Bruck apartment complex in Changxing, China, completed in 2012, is one of the first large-scale passive house projects in Asia. This five-story building contains 36 apartments and was designed to meet the Passive House standard while adapting to local climate conditions and construction practices. The project demonstrates that passive house principles can be successfully applied in China's construction industry, potentially paving the way for more widespread adoption of these energy-efficient building techniques in the rapidly developing country.
Belfield Homes social housing project in Dublin, Ireland
The Belfield Homes project in Dublin, completed in 2017, is Ireland's largest certified Passive House development to date. This social housing project consists of 59 homes designed to Passive House standards, providing high-quality, energy-efficient housing for low-income residents. The project showcases how passive house principles can be applied cost-effectively in social housing, delivering long-term benefits in terms of reduced energy costs and improved comfort for residents.
These case studies highlight the versatility and effectiveness of passive house design across different climates, cultures, and building types. From single-family homes to large-scale developments, passive house principles are proving to be a powerful tool in creating sustainable, comfortable, and energy-efficient buildings worldwide.